Historias Reales: Accidentes Laborales Que Marcaron un Antes y un Después
Descubre tres impactantes relatos de accidentes laborales reales que pudieron haberse evitado con medidas básicas de seguridad y mantenimiento. Desde un derrumbe en una mina hasta tragedias en fábricas y construcciones, este blog analiza las causas, las consecuencias y las lecciones que debemos aprender para prevenir futuros desastres. La seguridad laboral no es un gasto, es una inversión en vidas y productividad. ¡No te pierdas estas historias que te harán reflexionar!
Mtr. S.H.yP.A. Daniel Ornelas Ruiz
11/18/20243 min read
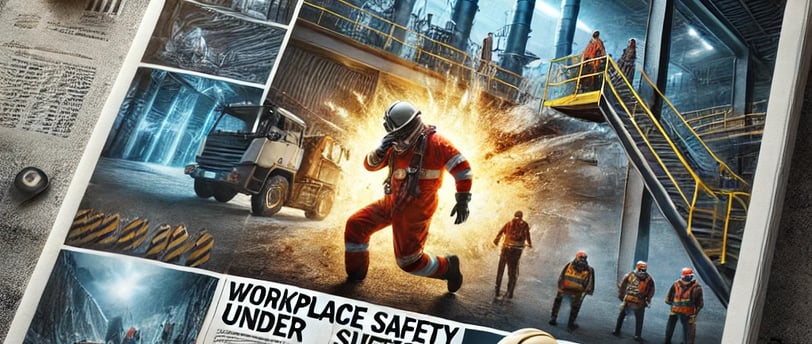
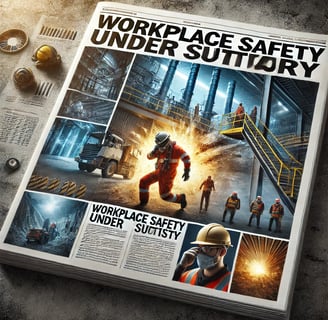
Historias Reales: Accidentes Laborales Que Marcaron un Antes y un Después
La negligencia en medidas de seguridad y mantenimiento no solo afecta la operatividad de las empresas, sino que también pone en peligro la vida de los trabajadores. A continuación, te presentamos tres casos reales y documentados que resaltan la importancia de la prevención en el ámbito laboral.
1. Derrumbe en una mina por falta de inspecciones regulares
En 2010, la mina de San José, en Chile, fue escenario de uno de los accidentes más impactantes en la historia de la minería. Un derrumbe dejó atrapados a 33 mineros a 700 metros bajo tierra durante 69 días.
¿Qué ocurrió?
La mina ya había sido clausurada en años anteriores por problemas de seguridad, pero fue reabierta sin implementar mejoras sustanciales. Los informes señalaron que la falta de un sistema de soporte adecuado para los túneles y la omisión de inspecciones regulares fueron los factores clave que llevaron al colapso.
Consecuencias:
Aunque todos los mineros sobrevivieron gracias a un rescate internacional, muchos enfrentaron secuelas físicas y psicológicas. Este caso resaltó la necesidad de un cumplimiento estricto de normas de seguridad y revisiones periódicas en entornos de alto riesgo.
Lecciones aprendidas:
La minería es una actividad intrínsecamente peligrosa, pero los riesgos pueden minimizarse con medidas como:
Inspecciones regulares de las condiciones estructurales.
Sistemas de monitoreo en tiempo real para detectar inestabilidades.
Capacitación constante del personal en protocolos de emergencia.
2. Aplastamiento en un sitio de construcción
En Nueva York, un trabajador fue fatalmente aplastado entre una excavadora y una pared en un proyecto de construcción. El operador no notó su presencia debido a un punto ciego, lo que resultó en un desenlace trágico.
¿Qué ocurrió?
La investigación reveló que la maquinaria no estaba equipada con sistemas de cámaras o sensores para puntos ciegos. Además, no se designó a un observador que guiara al operador durante las maniobras.
Consecuencias:
Este accidente resultó en una multa significativa para la empresa y una revisión de sus prácticas de seguridad. A nivel personal, la familia del trabajador enfrentó una pérdida irreparable.
Lecciones aprendidas:
Las zonas de construcción son especialmente propensas a este tipo de accidentes. Medidas que podrían haber prevenido esta tragedia incluyen:
Equipar maquinaria con tecnología de monitoreo de puntos ciegos.
Establecer zonas de seguridad estrictas alrededor de las máquinas en operación.
Realizar capacitaciones específicas para operadores y observadores.
3. Golpe mortal en una fábrica por maquinaria en mal estado
En una planta de manufactura en Detroit, un trabajador fue alcanzado por el brazo mecánico de una máquina industrial, que falló debido a un mantenimiento deficiente.
¿Qué ocurrió?
La máquina, una prensadora de piezas metálicas, llevaba meses funcionando con irregularidades detectadas por los operadores, pero la empresa no priorizó las reparaciones. Durante una jornada rutinaria, el sistema de frenos falló, haciendo que el brazo mecánico se moviera de forma descontrolada y golpeara al empleado.
Consecuencias:
El trabajador sufrió lesiones graves que le provocaron incapacidad permanente. La fábrica tuvo que enfrentar demandas legales y costos de reparación que superaron con creces el costo inicial de un mantenimiento adecuado.
Lecciones aprendidas:
Los accidentes con maquinaria industrial suelen ser evitables mediante:
Programas de mantenimiento preventivo regulares.
Auditorías de seguridad externas para garantizar el cumplimiento normativo.
Sistemas de apagado de emergencia accesibles para los operadores.
Reflexión Final
Cada uno de estos casos demuestra que los accidentes laborales son casi siempre prevenibles. La inversión en seguridad y mantenimiento no solo protege vidas, sino que también evita pérdidas económicas y legales para las empresas.
La seguridad laboral no es negociable. ¿Tu empresa está haciendo todo lo necesario para garantizarla?
Referencias
BBC News. (2010). Chile mine rescue: The extraordinary story of the 33. Recuperado de https://www.bbc.com/news
Occupational Safety and Health Administration (OSHA). (2021). Accidents in construction: Causes and prevention. Recuperado de https://www.osha.gov
National Institute for Occupational Safety and Health (NIOSH). (2020). Workplace safety and machinery failures. Recuperado de https://www.cdc.gov/niosh/
Greenberg & Stein. (n.d.). Accidents involving heavy machinery in construction sites. Recuperado de https://www.greenbergandstein.com
Capacitación
Asesoría y tramites en materia de seguridad e higiene industrial y salud ocupacional.
Telefonos
para mas informacion:
Blvd. Huapango 17942 Int.102D, Col. Los Reyes. C.P. 22125, Tijuana B.C.
Cell. (52) 661 266 5537
© 2024. All rights reserved.
Ubicanos
Office. (52) 664 738 6367
WhatsApp. (52) 661 266 5537
siguenos en redes